Energy Management Systems
An Energy Management System (EMS) is a comprehensive system designed to monitor, control, optimize energy performance and usage patterns within a commercial, industrial, and residential facility, building or organization.
The primary goal of an EMS is to improve energy efficiency, reduce energy costs and minimize environmental impact by real-time monitoring and analysis of energy consumption data, providing insights into energy usage patterns and potential energy savings, finding areas of inefficiency, and implementing strategies to improve energy performance. It integrates hardware, software, and services and typically includes components such as sensors, meters, data loggers, control devices, and software platforms. EMS can automate processes like lighting, heating, ventilation, and air conditioning (HVAC&R) systems to operate more efficiently based on factors such as occupancy, temperature, and time of day.
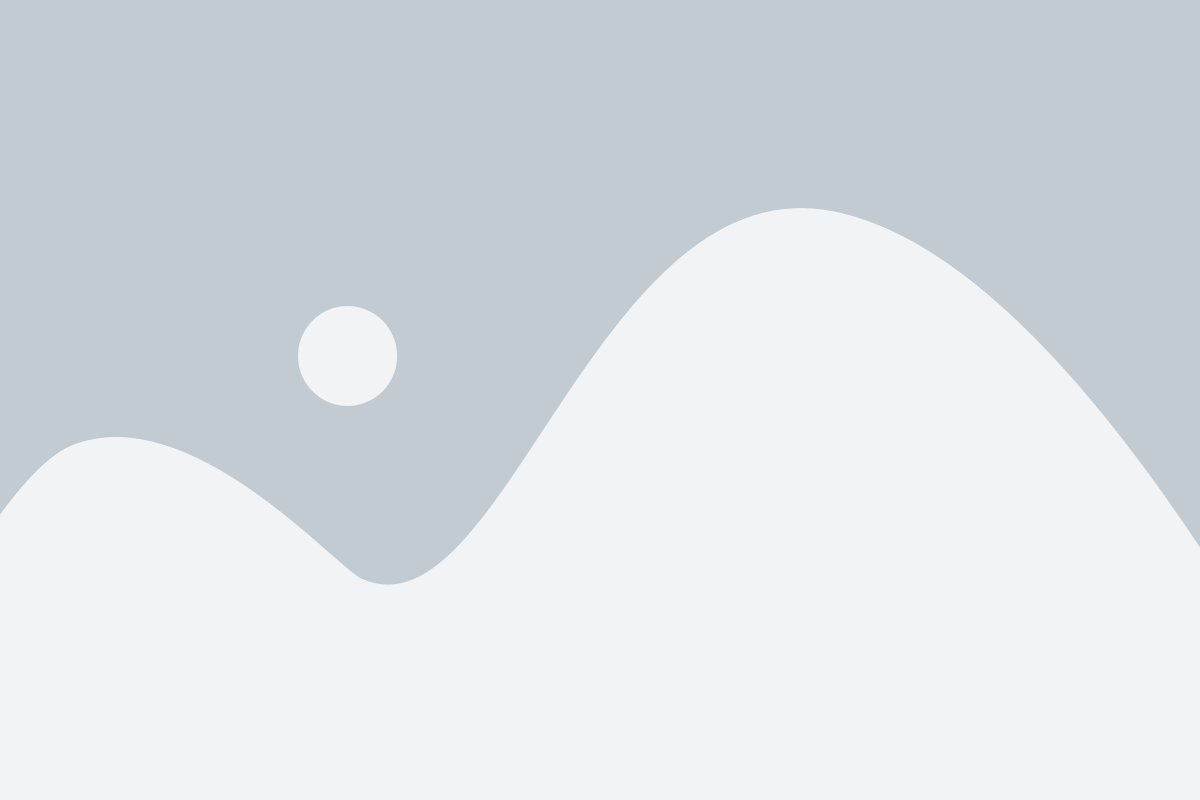
Key features of DURREL EMS Services
- Data acquisition, energy benchmarking, performance tracking and reporting: Durrel EMS is versatile and capable to perform data acquisition from various sources, such as energy meters, sensors, and building automation systems, to collect real-time information on energy consumption, demand, and environmental conditions and perform monitoring and analysis of energy consumption. The collected data is analysed to identify trends, patterns, and anomalies in energy usage. This enables us to understand how and when energy is being consumed within their facilities.
- EMS generate reports, dashboards, and visualizations to present energy consumption data in easy-to-understand clear formats such as charts, graphs, and dashboards and actionable format to ease decision-making. This enables stakeholders to track performance metrics, monitor progress towards energy goals, and find areas for improvement. It enables comparing energy usage against historical data, industry standards, or peer organisations to find areas for improvement. They also facilitate tracking the effectiveness of energy-saving initiatives and generating reports to communicate results to stakeholders.
- Dynamic demand response, Load management, Energy conservation measures, Control and Automation: Our EMS incorporate demand response capabilities, load shifting, equipment optimization, enabling users to participate in utility programs or adjust energy usage in response to grid conditions or pricing signals. Load management features help optimize energy usage to minimize peak demand charges and avoid grid strain.
- Durrel EMS can integrate with other building management systems, including HVAC, lighting, security, renewable energy systems and utility networks, to provide a centralized platform for comprehensive energy management and control across multiple domains. EMS include control features that allow users to remotely manage and adjust building systems, equipment, and settings to optimize energy performance. This may involve automated scheduling HVAC (heating, ventilation, and air conditioning) operations, lighting controls, or equipment shutdown during periods of low demand.
Energy Modelling, Efficiency Audits and Feasibility Assessment
Durrel’s in-house experts will perform energy modelling and simulation of Industrial and commercial buildings, validating Building Design, HVAC&R system Analysis, Daylight analysis, Fenestration analysis, Life cycle cost analysis, water footprint assessment and waste management as per the compliance codes and others
Durrel facilitates the discovery of energy conservation possibilities in the plant by detailed study of the electrical distribution systems and electrical equipments. The Energy Audit includes the review of documentation with respect to the scope covered in audit, an on-site visit, data collection, data review & analysis, report preparation and submission. This will also require the cross check and verification of information and data which may include industry norms and peer data.
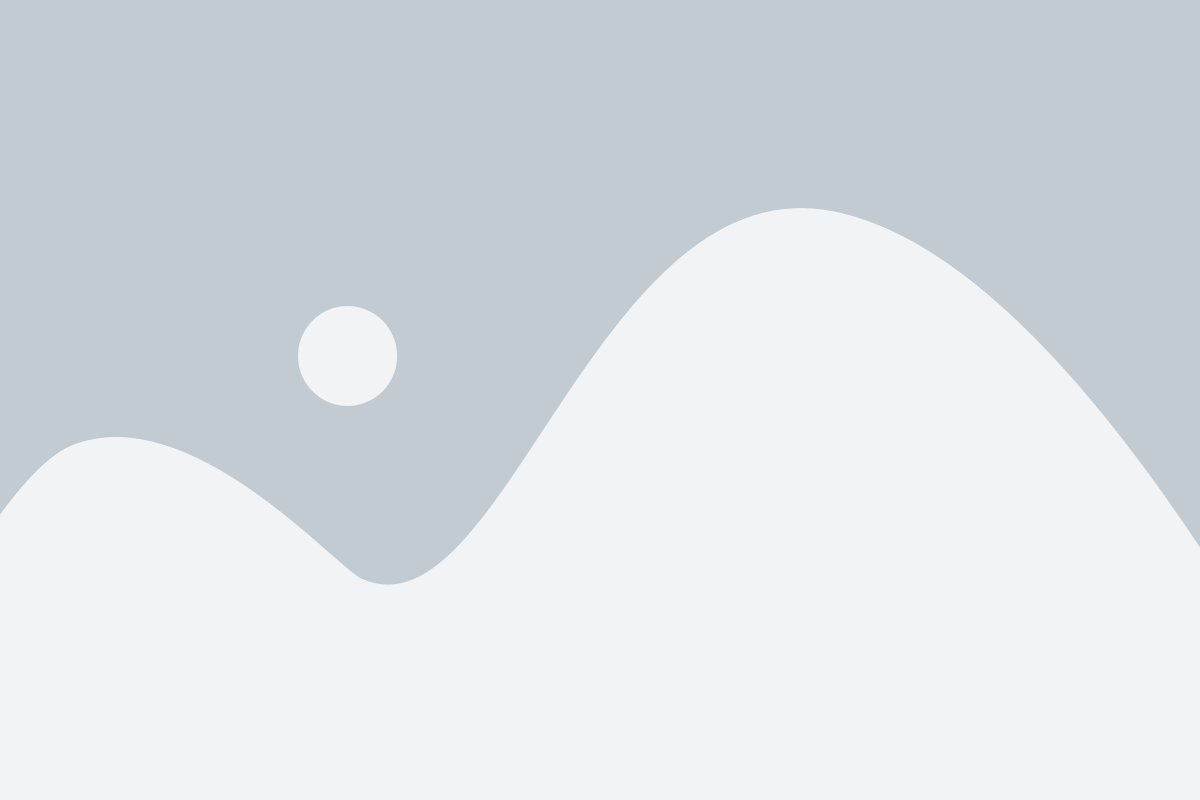
EMS Deployment Approach
- Establishing the energy consumption pattern and grade the level of infrastructure on the maturity model
- Measurement of incoming supply for 24 hours through 3 phase power analyzer and to understand the incoming power quality through online line recording of kW, Amp, Voltage, Power Factor, Harmonics in voltage and current
- Calculate the percentage loading of transformers
- Performance evaluation of electrical system such as Servo Voltage Stabilizer, Capacitor Bank, Motors having capacity more than 10 kW, etc.
- Performance Evaluation of all DG Sets, Blowers, Compressors, ACs, AHUs, Cooling Tower, Luminaries, Pumps and water system
- Review of one year electricity bills, Estimating the potential for energy saving
- Identifying the hotspots for attention, immediate and no cost or low-cost improvements and the areas that require more detailed assessment
Key Contents of the Report
- Suggest technology substitutions along with cost analysis of technology substitutions and suggest vendors
- Energy Transition Roadmap and Framework; Consulting and Deployment
- IoT based, cloud hosted energy usage monitoring, analysis and energy saving solutions
- Building Management System with control and monitoring of HVAC and integration with all packages of energy management.
- Integration of dehumidifiers, exhaust fans, ventilation units etc.
- Energy meter integration and energy management solution
- Lighting Control system and power Conservation Solution
- Integration of generators, UPS, STP, WTP, Pumps